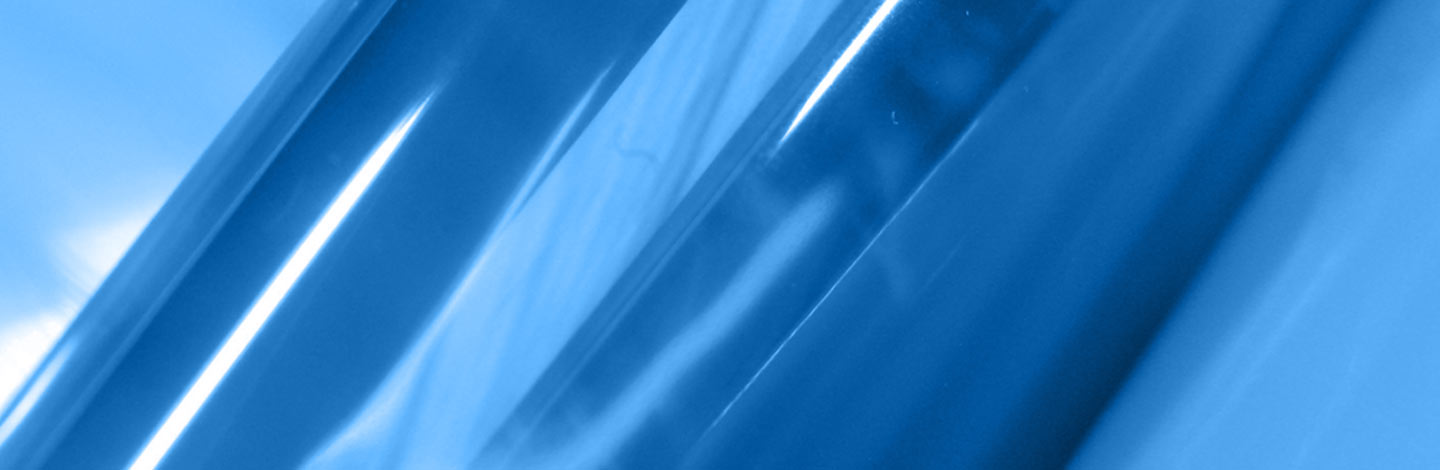
Pultrusion
Pultrusion is a continuous manufacturing process for tubes and profiles made of composite materials.
During this process, reinforcements (fibers, fabrics, etc.) packaged in coils are successively impregnated with resin and formed into the desired shape by passing them through dies heated to high temperatures.
The profile thus formed is pulled continuously by the pultrusion machine and cut directly to length at the line outlet.
The pultrusion process makes it possible to obtain profiles which, due to their characteristics, offer, under certain conditions, better guarantees than those made of steel or stainless steel.
Pultrusion allows the efficient and industrial production of high-performance composite parts with optimal quality :
- High fiber content
- Low level of porosity
- Excellent surface appearance, which does not require machining or finishing (“net shape”)
- Excellent repeatability and reproducibility from one production to another.
- Use of low-cost materials
- Continuous and automated process (low labor requirement)
- Possibility of customisation of the manufactured product
- Ability to easily create even complex geometries
This type of profile has a high specific mechanical strength (related to its weight), lightness, rigidity high fatigue and vibration resistance, oxidation and corrosion resistance, low thermal expansion coefficient and durability.
Various areas of application :
- Underground storage tanks: anchor straps, FAST fiberglass anchor base
- Refining of non-ferrous metals: equipotential insulators, electrolytic cells
- Electricity: bars for connection supports
- Pultruded and composite parts: Bars, rods and custom profiles
- Civil engineering: beams, floors
- Industrial poles: tubes, pipes